Neue Außenflügel B13e
Mit dem Erstflug eines Prototypen beginnt die Zeit der Flugerprobung. Die vorläufige Verkehrzulassung (Permit to Fly) ermöglicht es, Flugeigenschaften zu testen und für die Zulassung zu dokumentieren. In diesem Prozess befindet sich gerade unsere B13e.
Sie wurde schon viel und gerne geflogen: Testpilot:innen berichten, sie verhielte sich gutmütig und ausgeglichen im Flug, dazu sei sie sehr wendig trotz ihrer Größe. Auch das Projekt Motorisierung ist abgeschlossen. Und es wird weiter optimiert: Neben einer besseren Bremsklappenleistung, die mit dem Einbau der neuen Bremsklappen erzielt wurde, soll auch die Bodenfreiheit der Flächenspitzen erhöht werden.
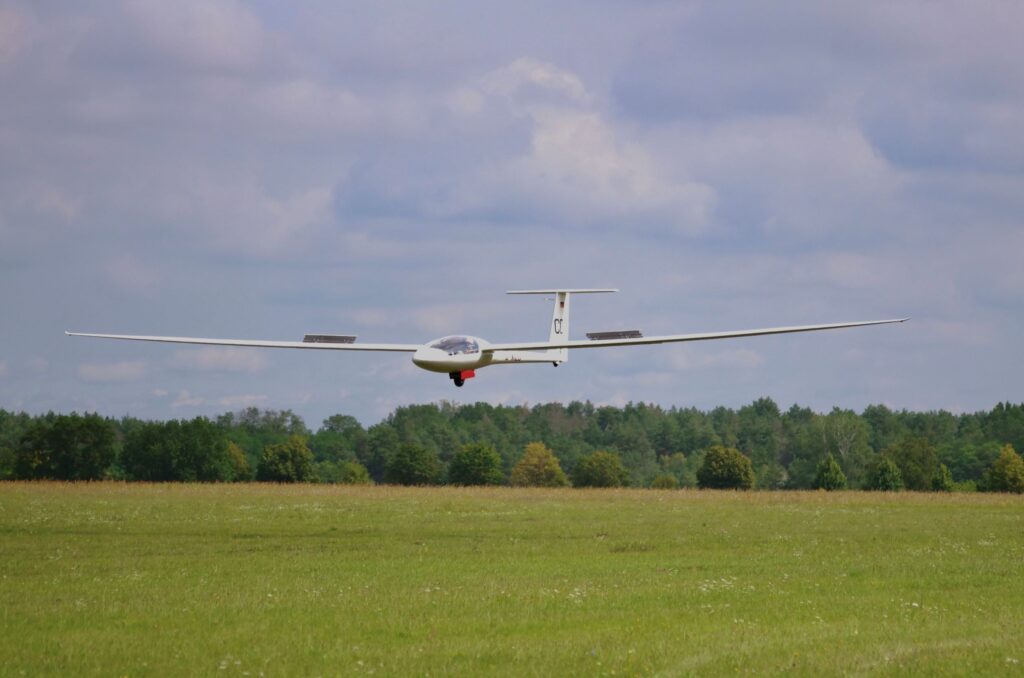
Der Bodenfreiheitswinkel der durchgängig geraden Flügel liegt bei nur 5 Grad, zum Vergleich: im Discus b sind es etwa 8,5 Grad. Die Gefahr während Start oder Landung eine Fläche abzulegen ist relativ hoch. Gerade diese kritischen Flugphasen werden durch den außermittigen Sitzplatz des Side-by-Side-Cockpits der B13e zusätzlich erschwert und erfordern viel fliegerisches Geschick. Ein größerer Bodenfreiheitswinkel würde die Sicherheit erhöhen und unseren Prototypen einem breiteren Spektrum von Pilot:innen zugänglich machen.

Warum neue Außenflügel?
Die Entscheidung eine neue Flügelgeometrie zu entwerfen resultierte aus dem Ausschluss anderer Ansätze; Die Vergrößerung des vergleichsweise kleinen Fahrwerks der B13e (ASH25) und eine Repositionierung des Flügels wurden ausgeschlossen.
Den Flügel vertikal zu repositionieren und den Flügel-Rumpfübergang wie bei einer Stemme S10 oder S12 zu gestallten bringt wenig Sicherheitsgewinn (von 5 auf 6 Grad Bodenfreiheitswinkel). Dazu wäre eine aufwendige Umstrukturierung des Rumpfes unumgänglich. Kosten und baulicher Aufwand für eine Fahrwerksvergrößerung
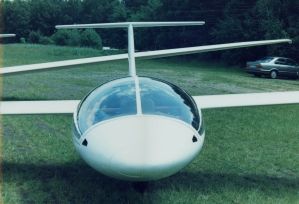
wären verhältnismäßig gering, allerdings wäre auch hier nur ein Grad an Bodenfreiheit gewonnen. Und ein weiteres Problem tut sich auf: Durch das größere Fahrwerk könnte der Bodenanstellwinkel erhöht werden und daraus eine verminderte Querruderwirksamkeit in Bodennähe folgen, was Sicherheitsrisiko vergrößern würde.
Die Flügelgeometrie zu verändern hält den konstruktiven und baulichen Aufwand jedoch überschaubar gering. Als beste Lösung bleibt also, die V-Stellung der Tragflügel zu vergrößern (s. Abbildung oben). Dazu können Innen- und Außenflügel neu entworfen oder jeweils nur die Flügelflächen an den jeweiligen Trapezenden „hochgeknickt“ werden, wie beim Arcus oder Ventus. Es zeigte sich nach Betrachten verschiedener Geometriekonfigurationen, dass eine Modifikation der Außenflügel (70% der Außenflügelspannweite) genügen würde, um den gewünschten Bodenfreiheitsgrad über 8 Grad zu erreichen. Als zusätzlicher positiver Nebeneffekt wird der Auflagepunkt der Flächen bei Bodenkontakt nach Innen verschoben. Die Flügelspitzenhöhe von nur 1,63m ermöglicht auch kleineren Pilot:innen das Aufrüsten.
Konstruktion und Bau zwei neuer Tragflügelformen sind kostenintensiv, weshalb wir uns für die notwendigen Formen und Faserhalbzeuge auf Unterstützung aus der Industrie setzen. In Folge der neuen Außenflügel müssen bestimmte Flugeigenschaften wie Trudelverhalten für die Zulassung erneut nachgeprüft werden. Das ist unproblematisch auf dem idaflieg Sommertreffen möglich.
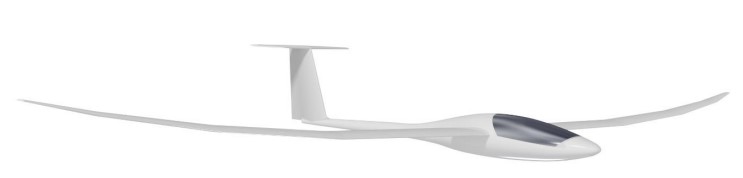
Die Simulation von Dreifach- und Vierfachtrapezflügelgeometrien ergab, dass letztere den Auftrieb der B13e potentiell verbessern könnte.
Zusätzlich soll eine Hängewinkelanzeige installiert werden, da sie kostengünstig und einfach umzusetzen ist. Sie unterstützt das Einschätzen besonders kleiner Hängewinkel und ist einfach ablesbar.
Vorentwurf
In seiner Bachelorarbeit zeigte Alex „Schrubb“ Hadzhiyski durch den Vergleich der zuvor vorgestellten Varianten, dass die am besten umsetzbare Lösung mit dem gefordertem Sicherheitsgewinn neue hochgeknickte Außenflügel sind. Berechnungen zufolge wird dadurch nicht nur die Flugsicherheit erhöht, sondern auch die Gleitzahl verbessert; Diese beschreibt das Verhältnis zwischen Horizontaldistanz und Höhenunterschied. Der Entwurf sieht einen Vielfachtrapez-Grundriss bei gleichzeitiger Erhöhung der V-Stellung vor.

Die Zulassungsvorschrift JAR-22 legt den Grundstein der neuen Außenflügel; Dabei werden gleichwertige oder bessere Eigenschaften, wie Überziehverhalten oder maximaler Auftrieb, gegenüber den alten B13e-Außenflügeln angestrebt. Zusätzlich muss der Entwurf mit allen Bauelementen der B13e harmonieren; Er unterliegt Stabilitätsanforderungen, die größtenteils mit dem Seitenleitwerk zusammenhängen, und darf die strukturelle Grenzen der Innenflügel nicht überschreiten.
Von den 19 untersuchten Neuentwürfen erfüllten einige die genannten Bedingungen, wobei sich der ausgewählte durch deutliche Steigerung der Flügelgleitzahl hervorhob. Ein Nachteil des Entwurfs liegt in der konstanten Verteilung des Auftriebsbeiwertes, die in der Theorie kein gutmütiges Überziehverhalten begünstigen; Diese war bezüglicher alten Außenflügeln jedoch weitaus kritischer. Und von der Gutmütigkeit der B13e in Trudel- und Überziehversuchen schwärmen bekanntlich alle Testpilot:innen.
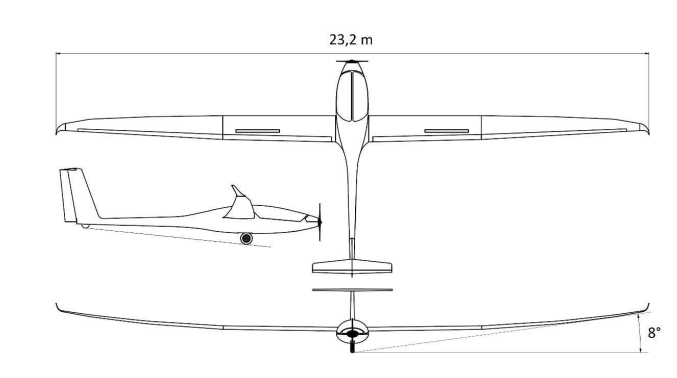
Nach der Bachelorarbeit erfolgten flugmechanische Untersuchungen zur Überprüfung der Stabilitätsmaßen des Gesamtflugzeugs, die zu Gunsten des Entwurfs ausfielen. Der Vorentwurf beeinflusst das Stabilitätsmaß nur geringfügig, weshalb der Schwerpunktbereich beibehalten werden kann. Großer Dank gebührt Marcus Golz, Schöpfer der Stemme S12-Winglets und guter Freund der Akaflieg, für die Unterstützung beim Entwurf der passenden B13e-Winglets.
Übung macht den Meister
Die Tragflügelkonstruktion der neuen Außenflächen soll in CFK-Bauweise, d.h. mit kohlefaserverstärktem Baustoff, realisiert werden. Dazu wird an der Strukturauslegung in diesem Jahr fleißig gearbeitet. Schon vor geraumer Zeit entstand der Plan, die Laminierkenntnisse im Verein aufzufrischen; Besonders was große Projekte angeht.
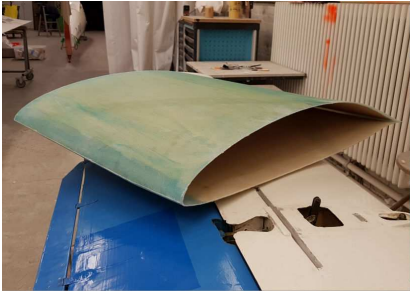
Es sollen einige Teststücke gebaut werden. Noch bevor wir eine eigene CNC-Fräse in der Werkstatt hatten, wurde eine Testform für den Außenflügelwurzelbereich gefertigt. Bei s-o-matec Sondermaschinentechnik in Pritzwalk halfen uns Jörg Zeiger und sein Team beim Umgang mit der Fräse, sodass wir nach vier Tagen eine fertige Form vorweisen konnten. Nach dem Finishen, Einkleben der Zentrierbolzen und Laminieren der Verklebefahnenform wurde das erste Test-Teststück gefertigt und schon bald sollen weitere entstehen: CAD-Modelle stehen zur Fertigung weiterer Formen bereit; Das Ureol für die Testformen fehlt jedoch. Unter anderem soll das komplette Innenleben einmal zum Test laminiert werden. Parallel werden Lastannahmen und Strukturberechnungen abgeschlossen.
Aufgrund der geringen Verfügbarkeit von Ureol entstand eine zunächst verrückt wirkende Idee – Lassen sich Negativformen aus 3D-gedruckten Teilen mit zufriedenstellendem Ergebnis herstellen?
Das Ergebnis ist hier zu lesen!
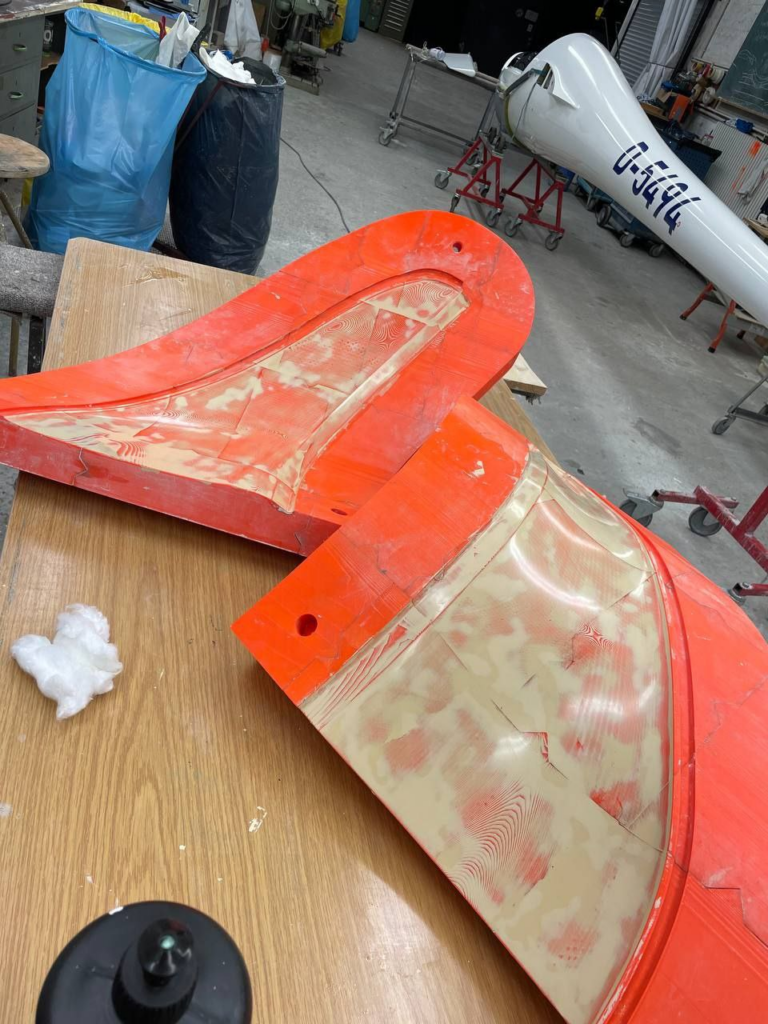
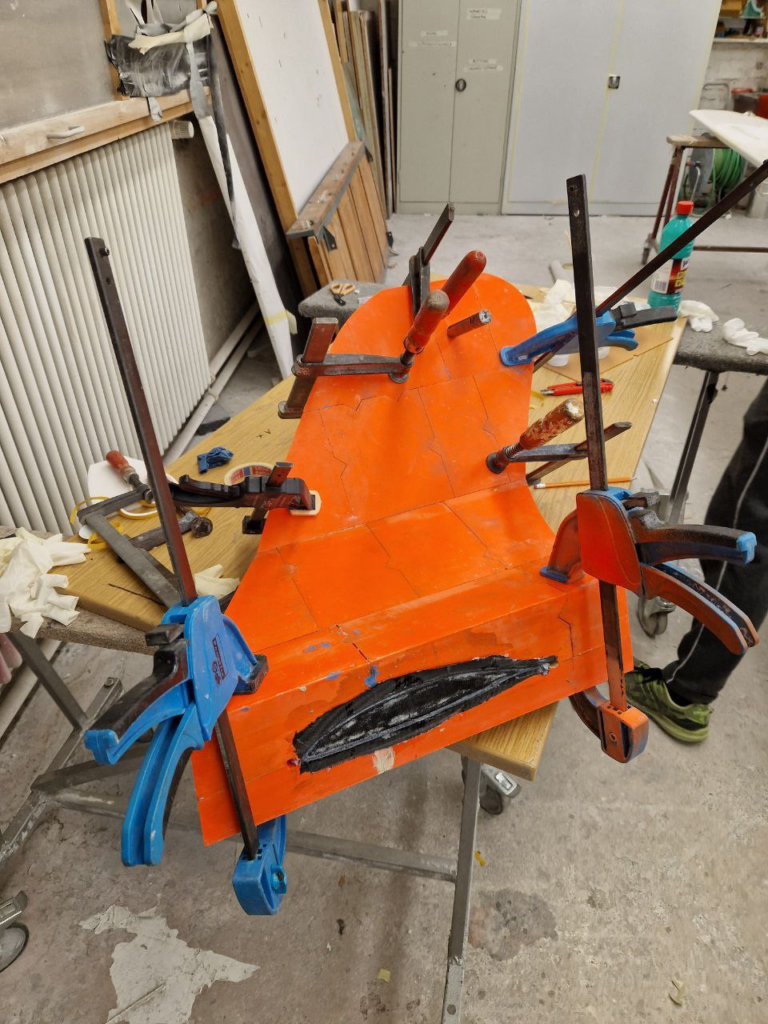
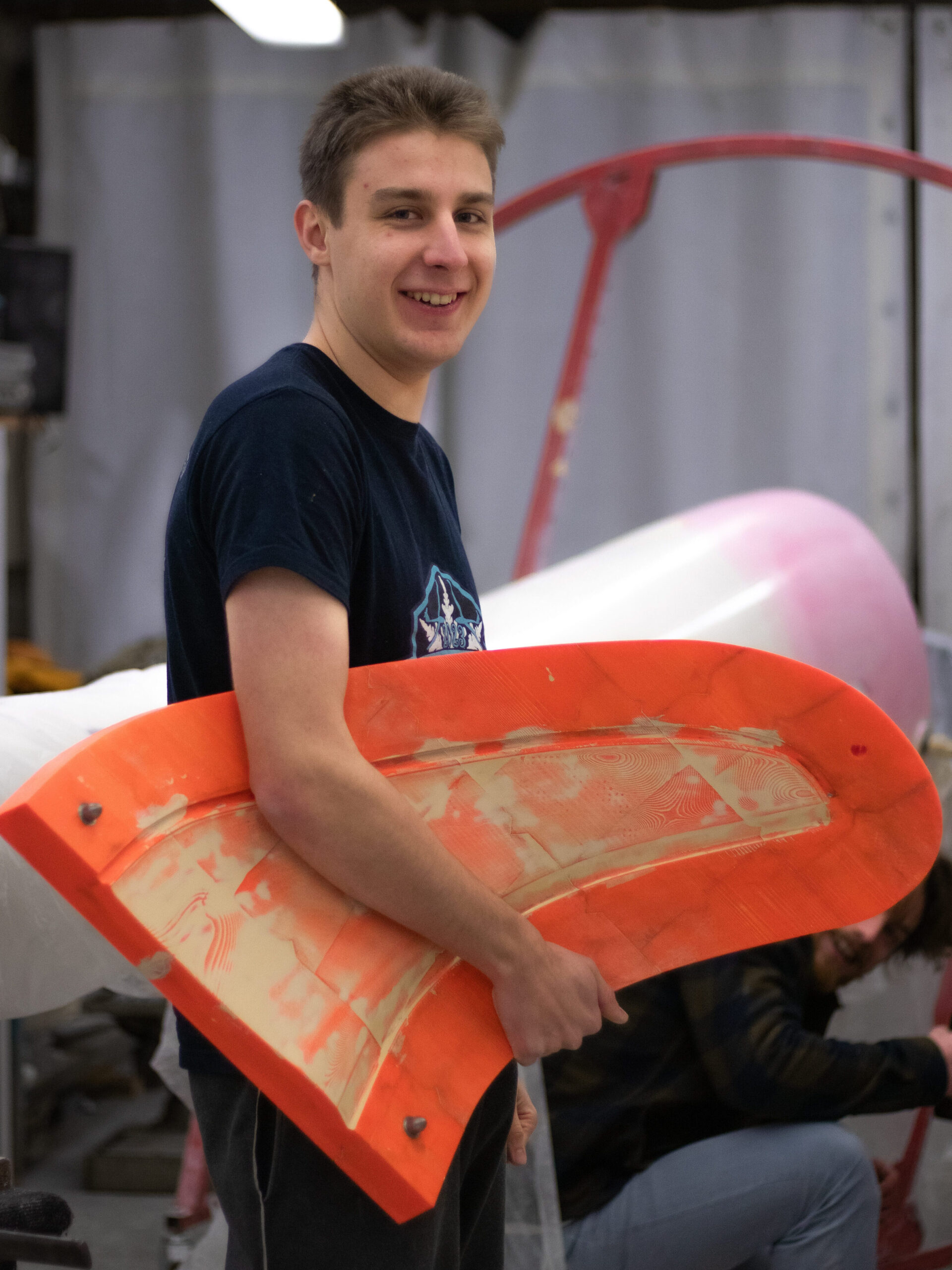