Wie führt man eine Projektweitergabe sinnvoll durch? Praktisch natürlich! Um neue Mitglieder im Konstruieren und Laminieren aus- und weiterzubilden, wollten wir das Winglet der neuen Außenflügel testweise bauen. Verfasst von David-Matthäus Dill:
Wingletform aus dem 3D-Drucker: Herausforderungen & Erfolge
Aufgrund der geringen Verfügbarkeit von Ureol entstand eine zunächst verrückt wirkende Idee – Lassen sich Negativformen aus 3D-gedruckten Teilen mit zufriedenstellendem Ergebnis herstellen? Zunächst stellten die begrenzte Größe und Auflösung des 3D-Druckers Schwierigkeiten dar. Auch die Dichtigkeit der Form bereitete uns Sorgen, da das Laminat unter Vakuum aushärten würde. Nach einigen Testdrucken und Vakuumtests waren wir dennoch optimistisch genug, um das Experiment 3D-Druck-Form zu starten. Die geringe Hitzebeständigkeit schloss frühzeitig PLA aus, die Wahl fiel auf PETG. Es wurden also 30 Formteile auf zwei 3D-Druckern parallel über eineinhalb Monate gedruckt.
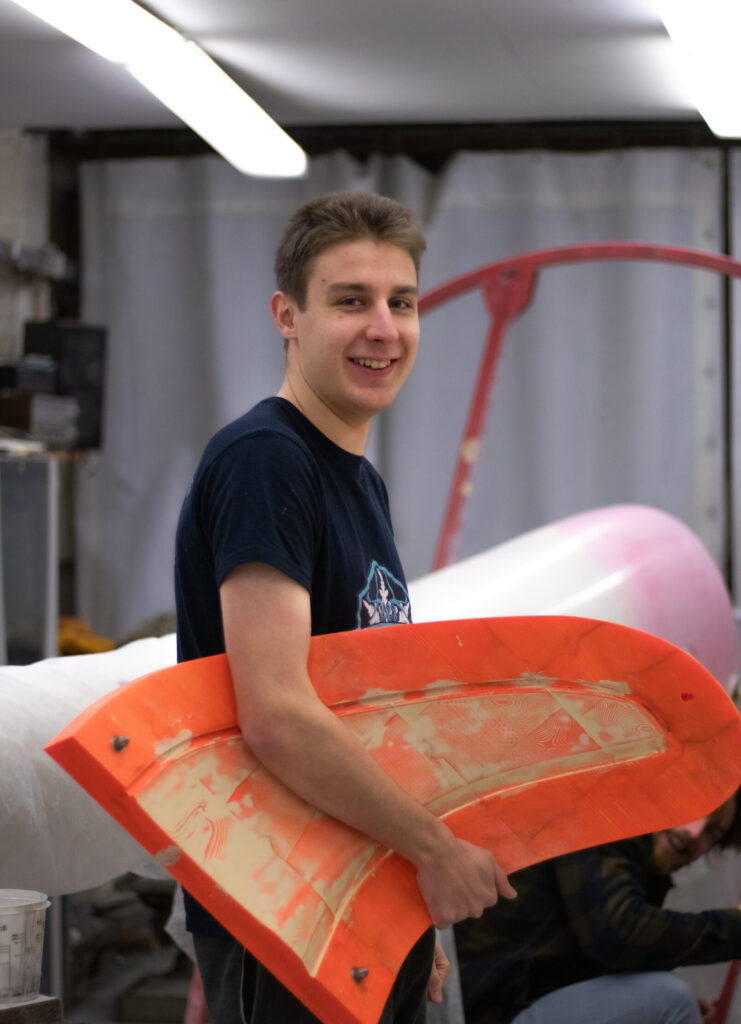
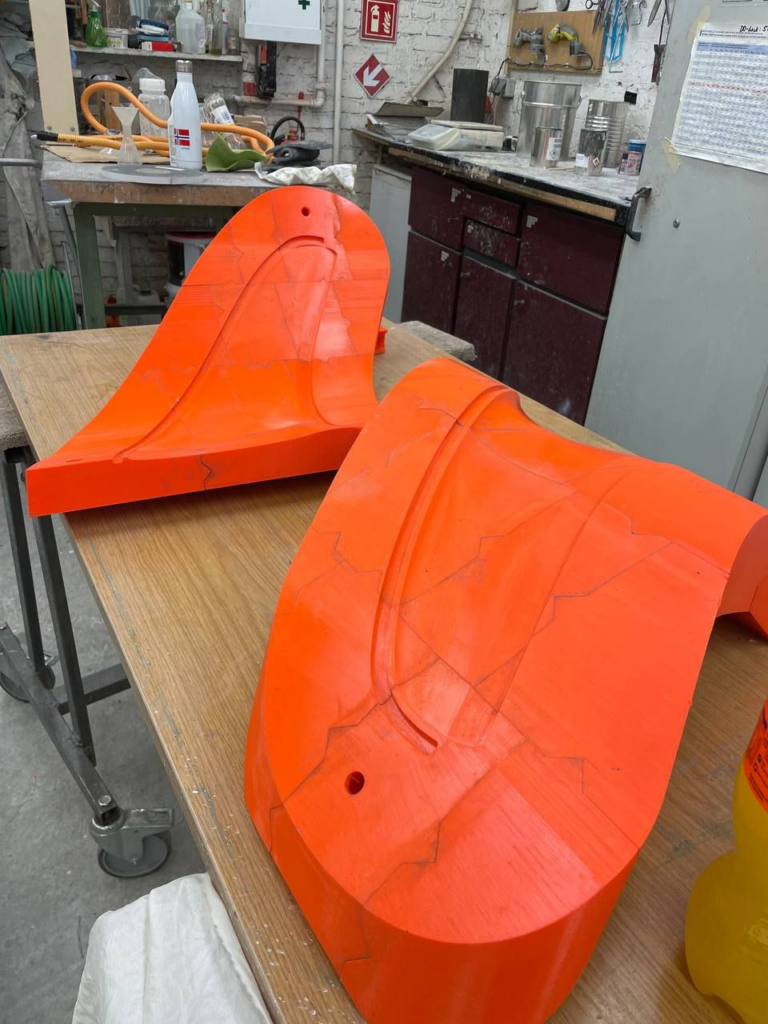
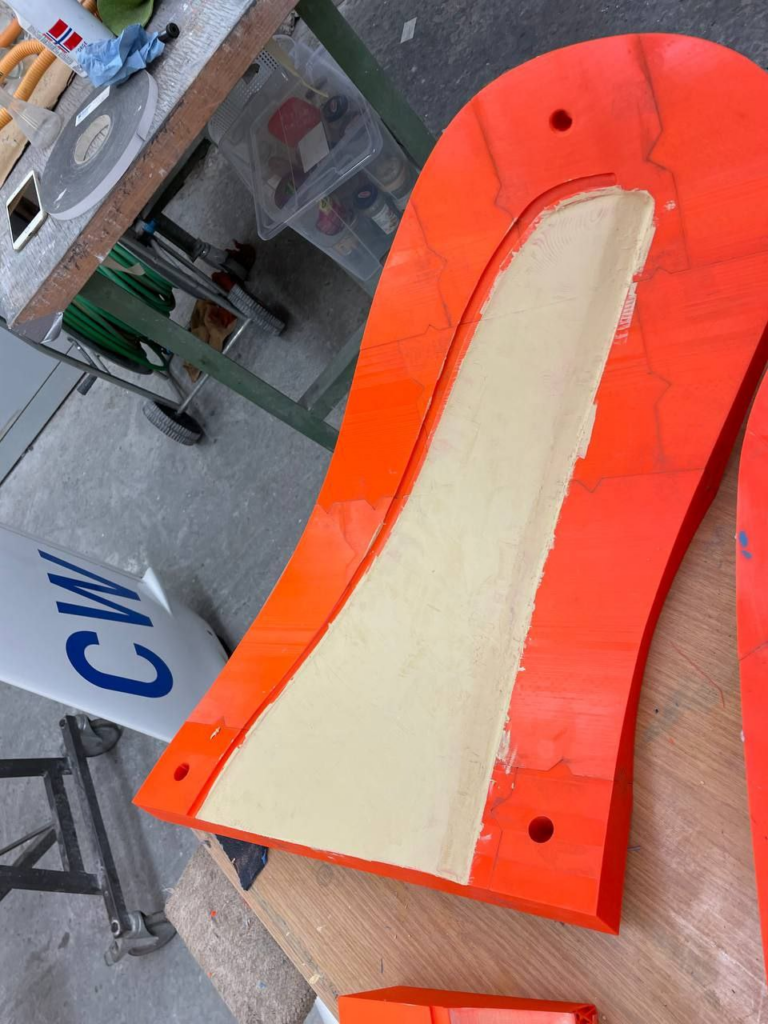
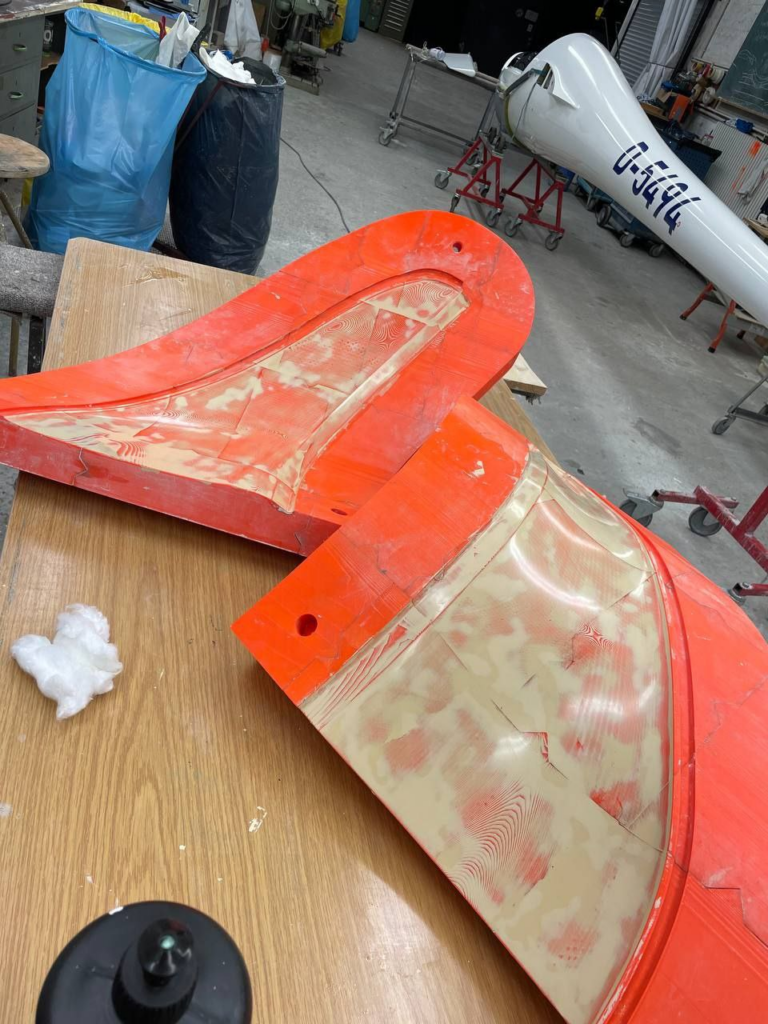
Kaum waren die Formteile fertiggestellt, stand das Verbinden der Einzelteile an. Schon hier machte sich die Ungenauigkeit des 3D-Drucks bemerkbar, denn das Zusammenpuzzeln der einzelnen Teile verlief nicht so reibungslos wie erhofft. Am Ende musste jedes Stück einzeln an die umliegenden Stücke angepasst werden. Ein Test zeigte, dass dickflüssiger Sekundenkleber zum Verkleben am besten geeignet war. Durch die Verklebungen war die Form jedoch nicht mehr dicht. Zusätzlich störten die Rillen, die durch den Herstellungsprozess auf der gesamten Form verteilt waren. Daher spachtelten und schleiften wir, bis eine gute und luftdichte Form vor uns lag. Zuletzt kam eine Form für die Wurzelrippe aus dem Druck. Kaum war eine Testbelegung festgelegt, war es auch schon so weit, wir konnten das erste Testwinglet in der 3D-gedruckten Form laminieren.
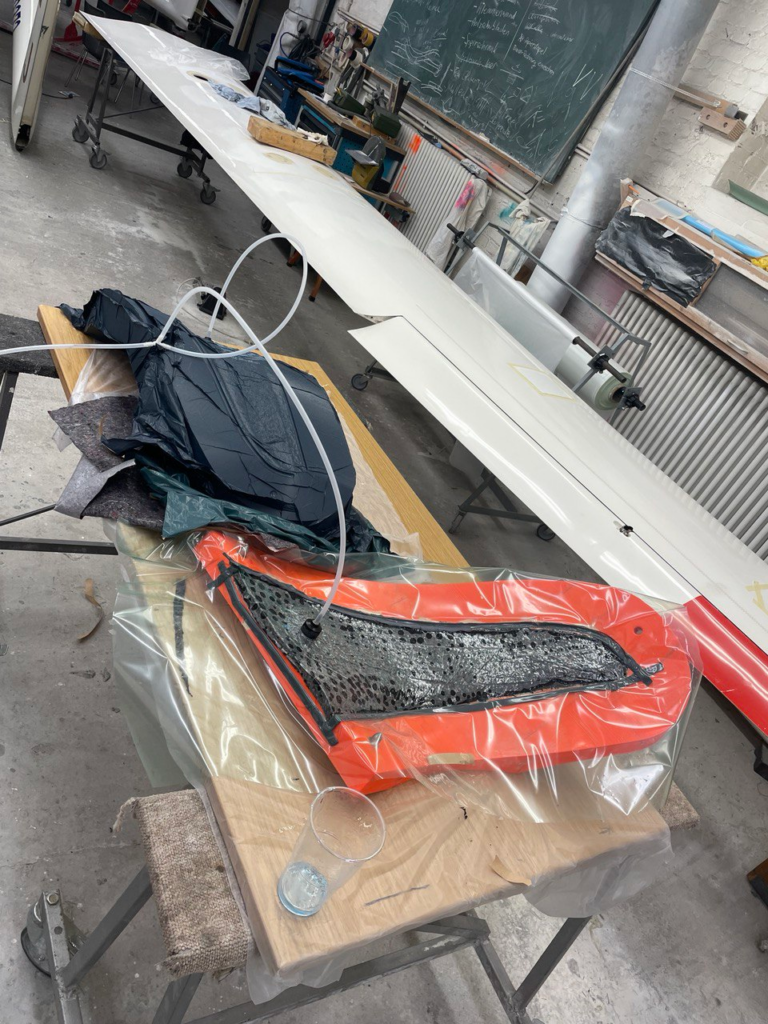
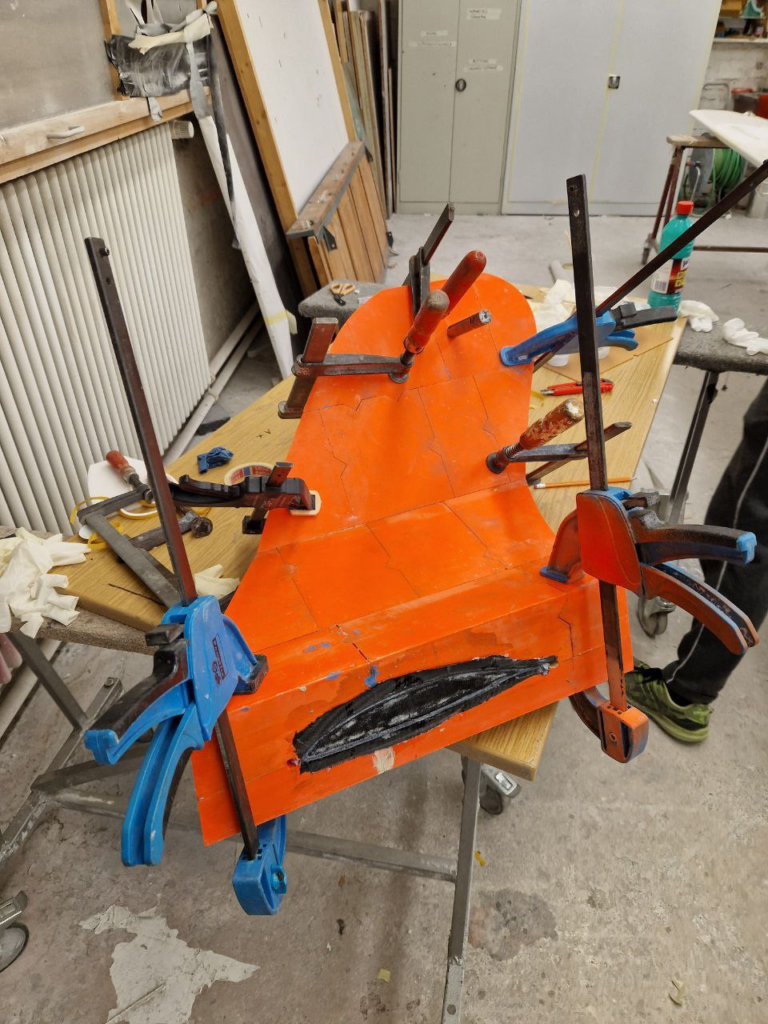
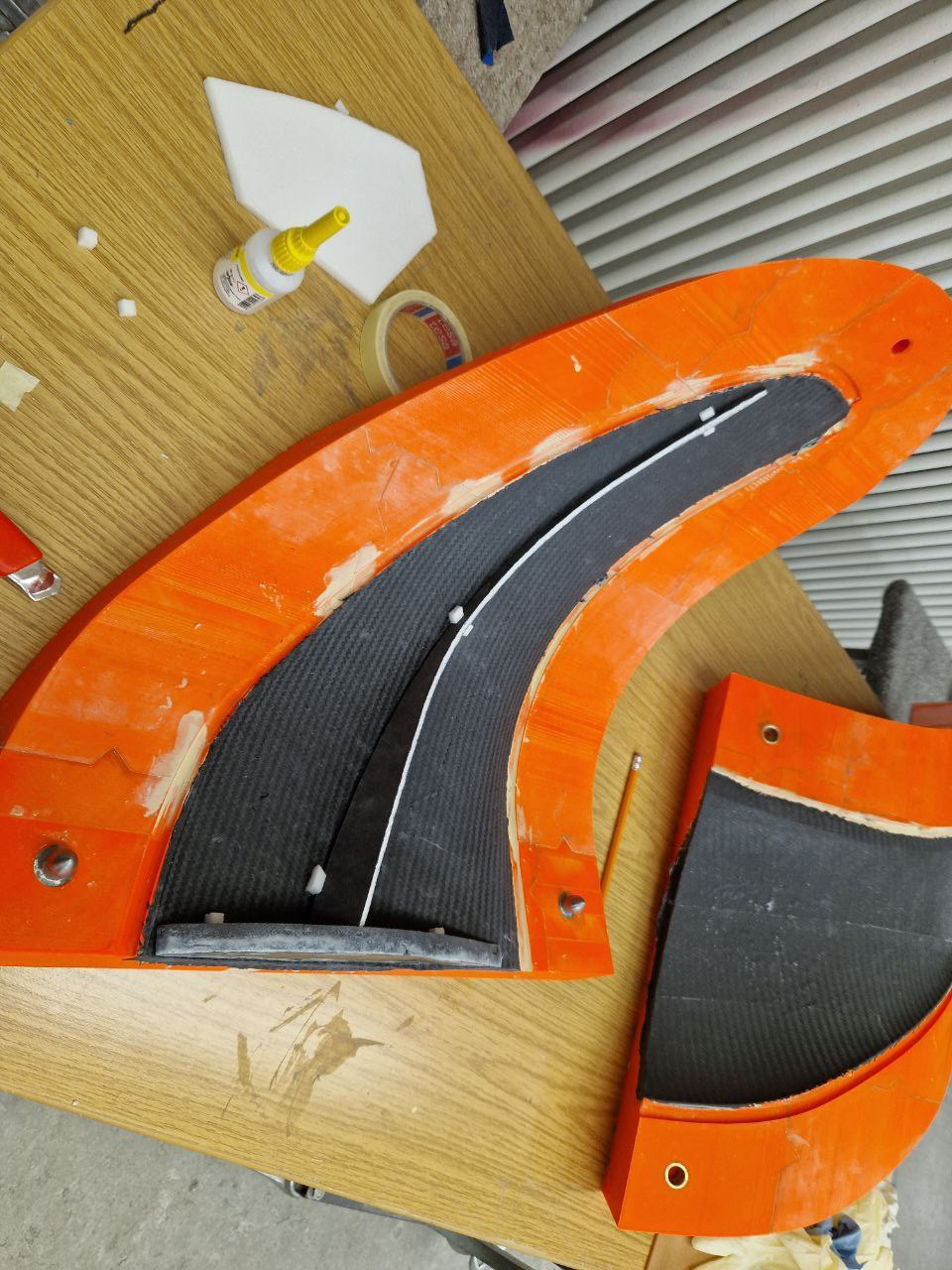
Das Resultat der Oberfläche überraschte uns positiv. Unser Fazit ist aber, dass der Aufwand zur Herstellung der Form nicht im Verhältnis zum Ergebnis steht. Die Ungenauigkeiten des 3D-Drucks auszugleichen war mühselig. Mit einem größeren 3D-Drucker wäre die Herstellung denkbar, allerdings stellt die Möglichkeit von Fehldrucken ein großes logistisches Problem dar.
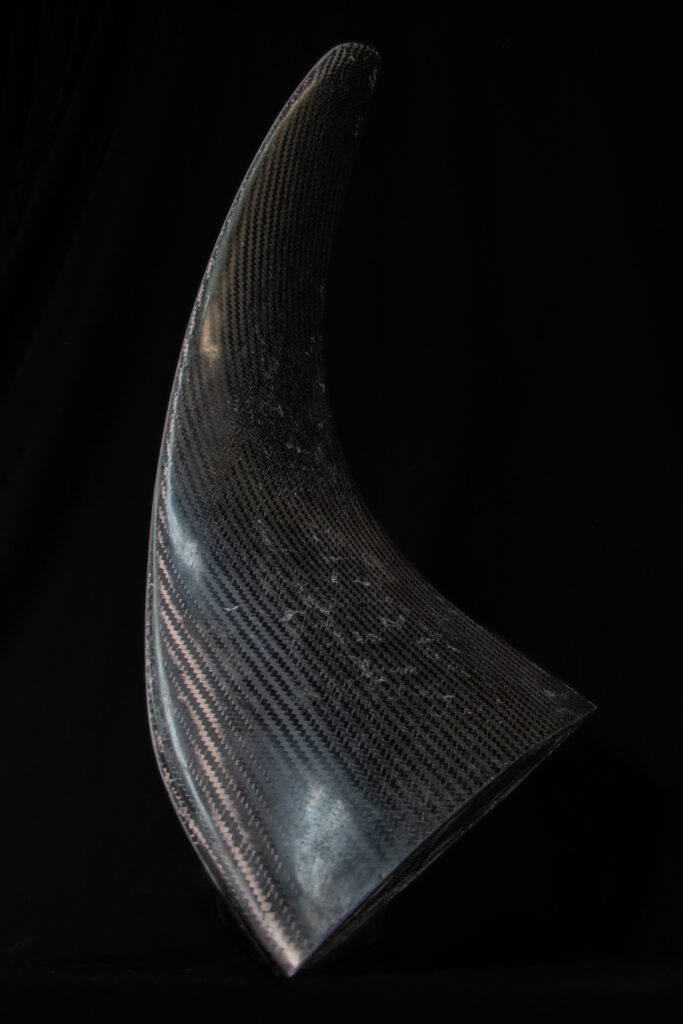
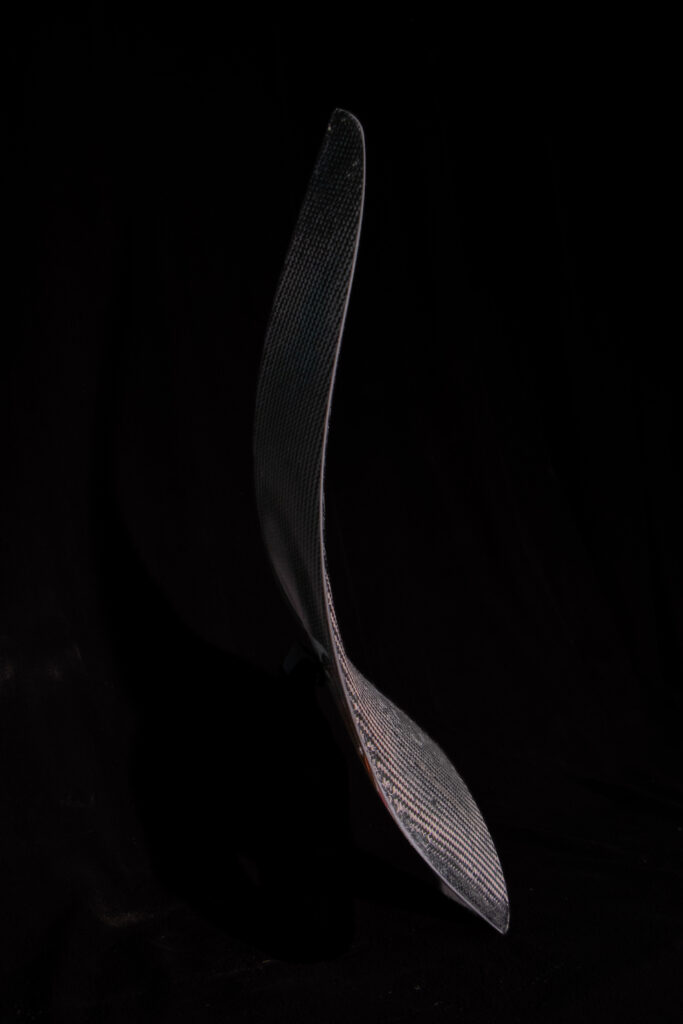
Schritte zur B13e-Zulassung
Wer fliegen will, kommt um Bürokratie nicht herum.
Auch die Zulassung der B13e geht voran. Das Problem einer jeden Akaflieg ist es, den Überblick über Projekte zu behalten, da diese teilweise über Jahrzehnte und mehrere Generationen laufen. Die B13e hatte 1991 ihren Erstflug, damals noch als B13 ohne den elektrischen Motor. Im Zuge der Flugerprobung fallen Flugeigenschaften auf, die optimiert werden sollten. So wurden bereits neue Bremsklappen entworfen und der Elektroantrieb entwickelt. Die B13e hat zudem Generationen erlebt, in der die Flugerfahrung in der aktiven Gruppe fehlte, um dieses beim Start und Landung anspruchsvolle Flugzeug fliegen zu können. Die B13 stand in dieser Zeit leider viele Jahre am Boden.

Aktuell sind wir dabei, sowohl fertige als auch angefangene Nachweise und Flugerprobungsprotokolle der B13e zu suchen und in einem übersichtlicheren System zu sortieren. In einer Liste über die Nachweisverfahren (Means of Compliance) wird mit dem Luftfahrtbundesamt (LBA) alles Nötige abgeklärt, um mit dem Bau der Außenflügel zu beginnen. Unser Ziel ist es, die B13e mit den aktuellen Außenflügeln zuzulassen, während wir parallel die neuen Außenflügel bauen. Die neuen Außenflügel werden dann als Änderung am Stück zugelassen.
Formen aus Malchow
Während in Berlin fleißig der 3D-Drucker mit Filament für die Wingletform gefüttert wurde, ging der Blick schon weiter auf die Formen der Außenflügel. Dafür wurden in einer Großaktion aus der Werkstatt von Leichtflugzeugbau in Malchow mit viel Muskelkraft alte Negativformen abgeholt. Von diesen wird das Gestell für die Außenflügelform der B13e übernommen.
Eine Woche nach der Besichtigung dieser besagten Formen ging es an einem verregneten Samstag mit einem großen Anhänger nach Malchow. Dort wurden die Formen per Hand aus der Werkstatt herausgefädelt und auf dem Hänger festgezurrt. In zwei Fuhren wurden die Formen sowie einige andere Fünde nach Kammermark überführt. Dort haben sie bis zu ihrem Einsatz ein vorläufiges Zuhause gefunden. Mit einigen weiteren nützlichen Dinge wurde zusätzlich zum großen Formenanhänger zweimal auch ein normalgroßer Anhänger voll bekommen. Pünktlich zum Sonnenuntergang waren alle wieder zurück in Kammermark und räumten alles ein. Einen großen Dank an Konrad Herz, welcher uns den Tipp gab, und alle fleißigen Helfer:innen.
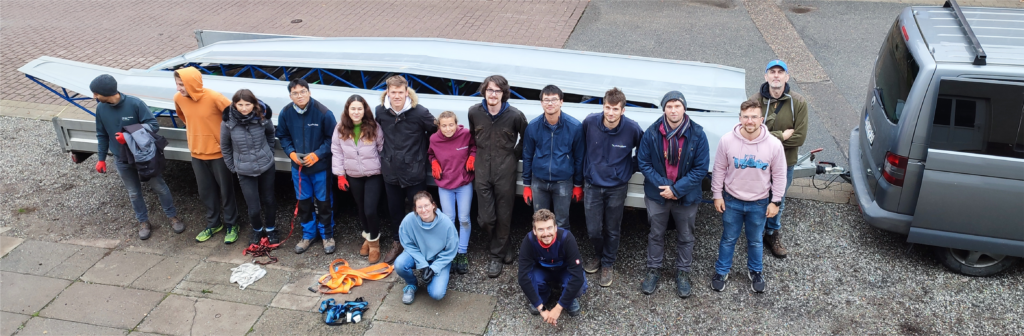
Wie geht es jetzt weiter?
Sobald das Winglet fertig auskonstruiert und mit der richtigen Belegung gebaut wurde, wollen wir erneut ein Testflügelstück mit allen Anschlüssen und Einbauten bauen. So üben und optimieren wir das Verfahren weiter, bis wir uns zutrauen, einen fliegenden Flügel zu bauen.
Das Stahlgestell der Außenflügel-Negativformen aus Malchow soll für unsere Außenflügelform weitestgehend übernommen und an unsere Flügelformen angepasst werden, da der Flügelgrundriss ähnlich zu unserem Außenflügel ist. Mit dem Bau der Formen soll dann begonnen werden, wenn die Liste über die Nachweisverfahren mit dem LBA besprochen wurde.