Verfasst von Yakumo Tomeda:
Wer die Akaflieg bereits kennt, weiß sicherlich, dass ein großer Aspekt unseres Vereins das Entwerfen und Bauen eigener Segelflugzeuge ist. Da klingt das Bauen eines Anhängers für die B12 – dem ältesten, noch flugtauglichen Prototyp der Akaflieg Berlin – vergleichsweise simpel, doch wie so oft bringt die Umsetzung mehr Herausforderungen mit sich als gedacht.
Segelflugzeuge und Anhänger
Doch erstmal einen Schritt zurück: Wieso ist ein Anhänger für ein Segelflugzeug überhaupt so wichtig? Segelflugzeuge verbringen weitaus mehr Zeit auf Autobahnen und Landstraßen, als viele vielleicht erstmal denken.
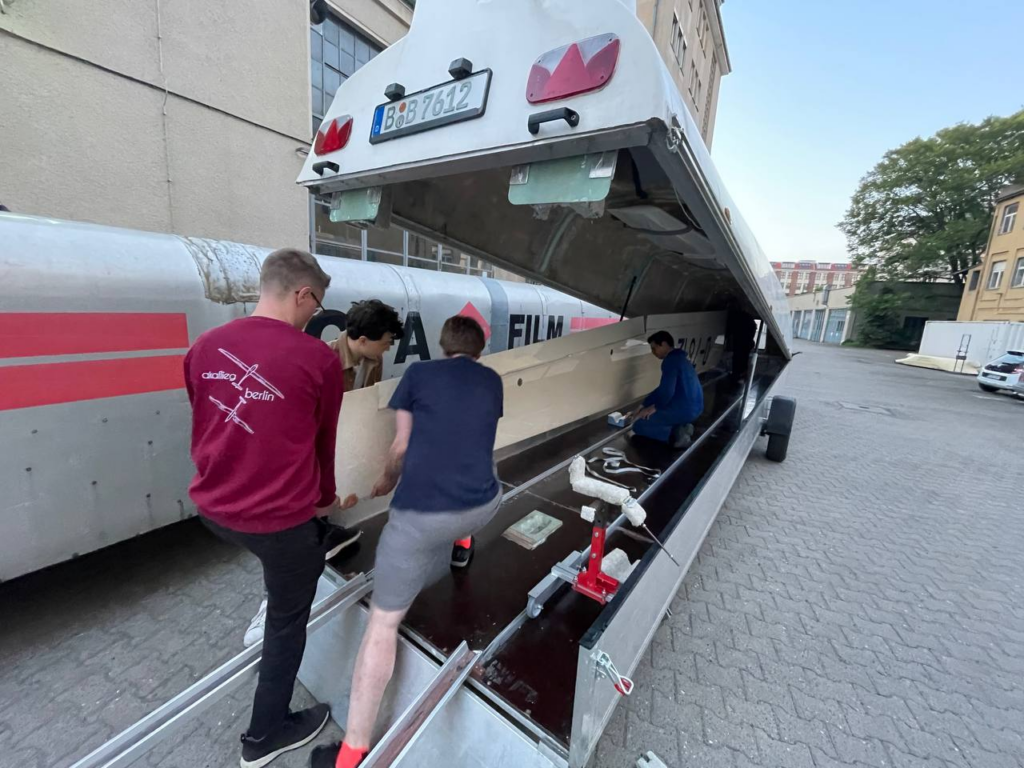
Nicht nur müssen sie regelmäßig zu Wartungs- und Reparaturzwecken in die Werkstatt gefahren werden, anders als ein Motorflugzeug können Segelflugzeuge nicht einfach zu diversen Events (Sommertreffen, Schimmelcup, Kunstfluglehrgang,….) an anderen Flugplätzen fliegen. Des Weiteren ist es nicht unüblich, dass ein Segelflugzeug bei einem Überlandflug eine Außenlandung hinlegt und entsprechend wieder von einem Acker zum Flugplatz befördert werden muss. Anders als große Verkehrsflugzeuge sind Segelflugzeuge auch dafür ausgelegt, schnell und einfach ab- und wieder aufgerüstet zu werden. Doch nicht nur das Flugzeug muss dies ermöglichen: Auch der Anhänger muss so ausgelegt sein, dass die einzelnen Flugzeugteile sicher verstaut sind und dass das Ein- und Ausladen, selbst auf einem Acker, ohne große Komplikationen ablaufen kann.
Was bisher geschah
Und so wurde Ende 2018 der B12 Anhänger, Marke Eigenbau ins Leben gerufen, doch es dauerte noch etwa ein Jahr, bis richtig Fahrt in das Projekt kam. Ende 2019 wurde eine Form für Anhängerdeckel besorgt, welche in typischer Akafliegmanier, nach etwas Schleifen und einigen Modifizierungen, einfach zum Deckel umfunktioniert wurde. 2020 kam dann die Pandemie, doch es ging weiter. Über den Sommer hinweg wurde der Unterbau des Anhängers am Flugplatz in Kammermark gebaut und anschließend mit dem Deckel verheiratet. Anschließend wurde er vom TÜV abgenommen und vom Flugplatz nach Berlin in die Werkstatt gebracht. Dort wurde, soweit es die Coronamaßnahmen zuließen, weiter gearbeitet und einige Fortschritte erzielt. Doch wie so oft bei der Akaflieg, stieß der Ehrgeiz auf seine Grenzen. Nicht alles funktionierte, wie man es sich vorstellte (der erste Rumpfwagen hielt einigen Belastungstests nicht stand) und das Projekt kam ins Stocken.
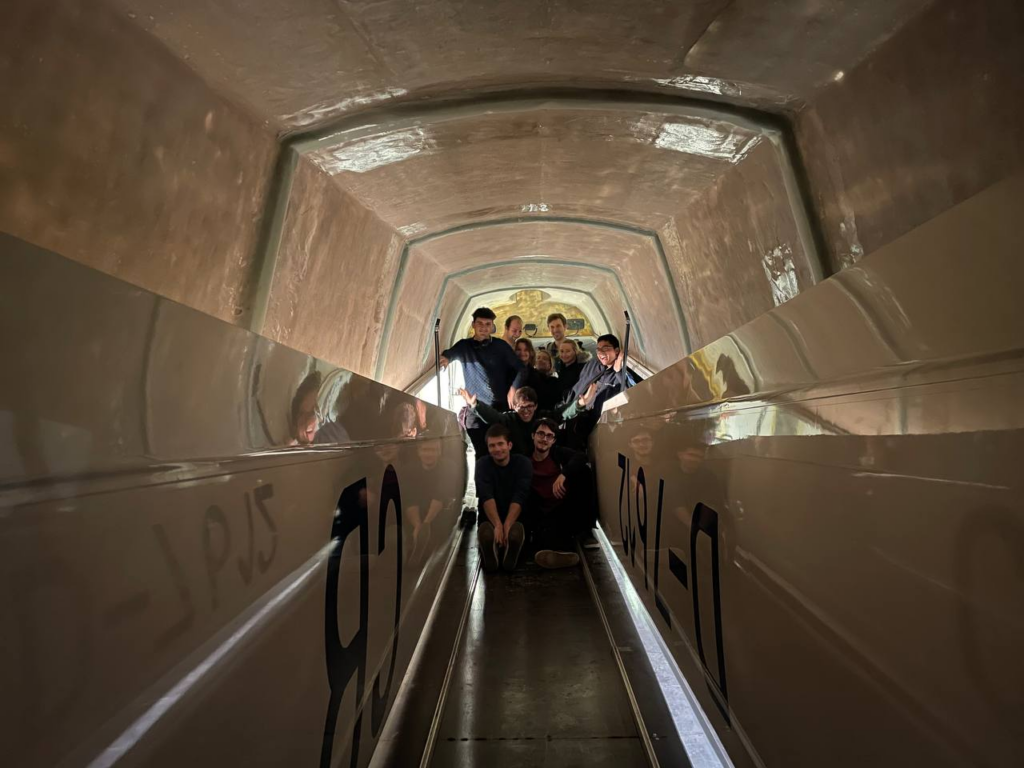
Optimierungsbedarf
Nach all den Jahren, wurde in der Wartungssaison 2023/2024 ein weiterer Anlauf gestartet, den Anhänger fertigzustellen. Natürlich wäre es kein Akaflieg-Projekt, wenn hierbei alles nach Plan laufen würde. Viele bereits fertiggestellte Teile wurden nochmals optimiert und verbessert. Nachdem sieben unserer Mitglieder beim Zellenwart in Stölln einiges über das Reparieren von Glasfaserlaminat und Lackschäden gelernt hatten, konnte dieses Wissen direkt in die Reparatur einiger Risse und Löcher im Deckel gesteckt werden. Für die Höhenleitwerkshalterung wurden vier Gewindebolzen kopfüber an die Innenseite des Deckels laminiert, eine ziemlich aufwändige Aktion. Leider kam es dann, wie es kommen musste: Der letzte Gewindebolzen riss in zwei Teile bei dem Versuch, einer Mutter noch ein kleines bisschen extra Halt zu geben. Nach viel verzweifeltem Gelächter, wurde getan, was getan werden musste: Das alte Laminat wurde mühselig weggeschliffen und erneuert, dieses Mal erfolgreich. Nach Fertigstellung der Flächenniederhalter und Flächenwagen wurde eine Fläche als Test eingeladen, wobei sich wiedermal Optimierungsbedarf zeigte.
Prio Nummer Eins
Kurz darauf wurde für das Projekt eine wichtige Entscheidung getroffen: Der B12-Anhänger sollte bis zum Abschluss vor allen anderen Projekten priorisiert werden. Darauf folgten einige sehr ertragreiche Arbeitstage, an denen fleißig am Anhänger mit großen Fortschritten gewerkelt wurde. Schon bald folgte jedoch das nächste Malheur: Ein Flächenwagen wurde beim Schließen des Deckels eingeklemmt und dabei wurde die Schweißnaht der Basis zerstört. Wie so oft ging es bei der Akaflieg zwei Schritte vor und einen wieder zurück.
Trotzdem ging es weiter. Immer wieder fand man sich in der Werkstatt ein, um Schritt für Schritt die Arbeit am Anhänger fortzuführen. Das Höhenleitwerk und die Flächen (wie so oft lief doch nicht alles nach Plan, und die Flächenlagerung ist noch nicht vollständig optimiert) sitzen mittlerweile sicher im Anhänger. Selbst beim Problemkind Rumpfwagen geht es voran. Sehr wahrscheinlich wird es noch die ein oder andere Komplikation geben, doch auch wenn der Ablauf nicht geradlinig ist, wird das Projekt in naher Zukunft fertig werden. Einerseits war es wichtig, das Projekt zu priorisieren, andererseits haben Deadlines klare Ziele vor Augen geführt. Diese und weitere Lektionen aus dem Projekt werden hoffentlich bei der Fertigstellung weiterer Projekte hilfreich sein und schon bald zur Fertigstellung des B12-Anhängers führen.
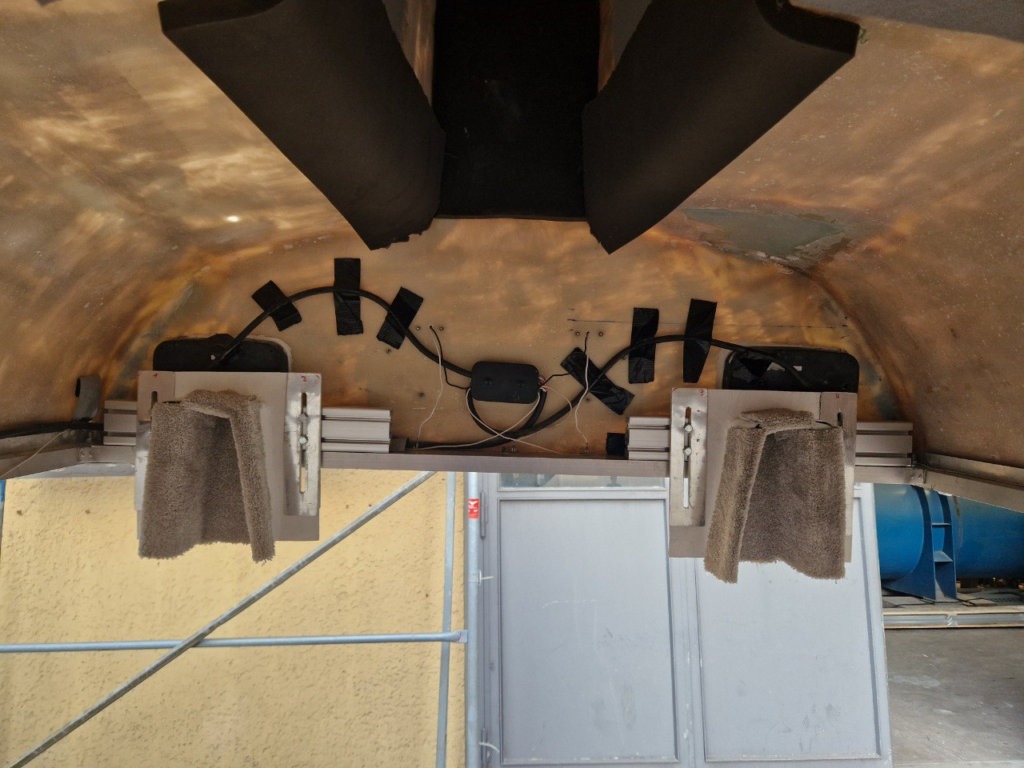
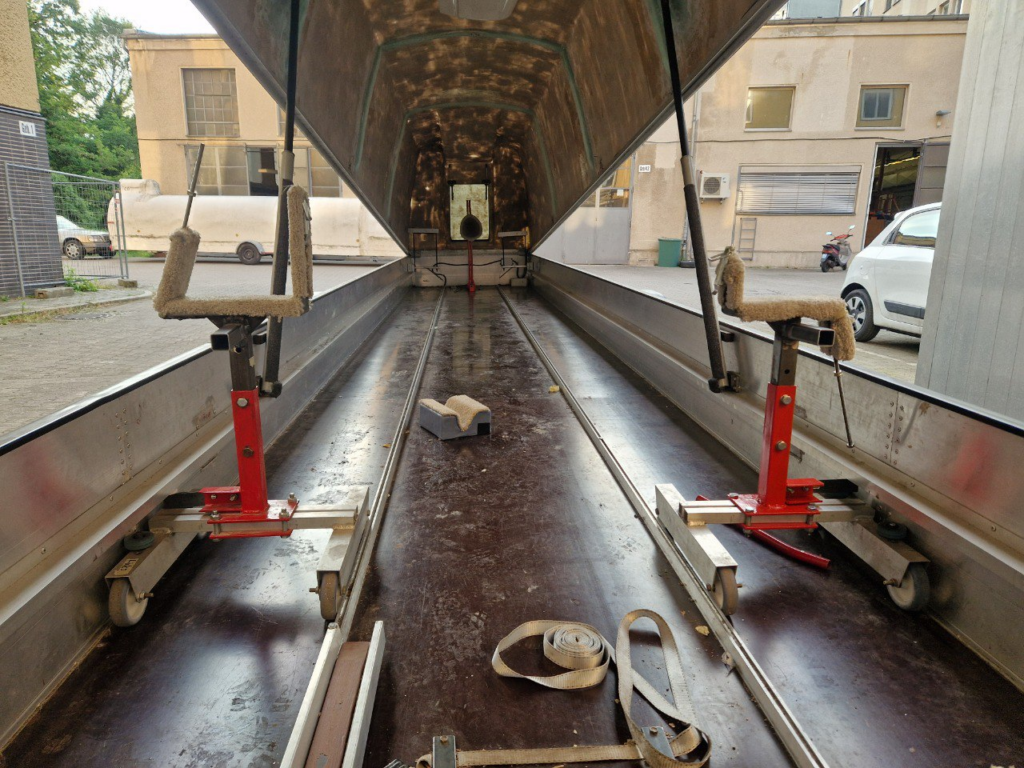